ABOUT US
If you need glass for your auto, home or business you can trust Hatchett Glass to take care of your needs. We have been locally owned and operated for 23 years in the Knoxville area. Our goal is to provide outstanding glass replacement services and quality with the best craftsmanship, products and materials available to the industry. Whether it’s replacing your windshield or replacing storefront windows or shelving, we provide the best value for our customers.
Dependability, quality and service are the mainstay of our growing business. Our client base is diversified, including insurance companies, dealerships, fleets and retail customers.
We have the expertise to service your needs whether your project is large or small. You will find that our service technicians are both professional and knowledgeable.
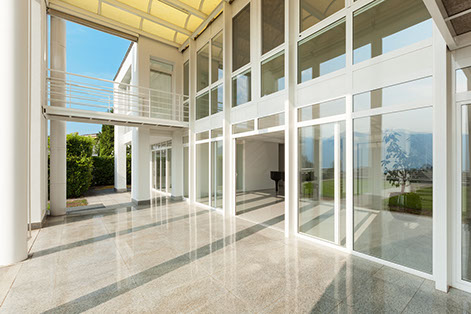
OUR GOAL
We aim to provide a quality service that exceeds our customers' expectations while being a leader in our industry through high moral standards and dedication to improving our business.
TYPES OF GLASS
We work with a wide range of different types of glass materials in our commercial and residential products.
Flat glass is the basic material that goes into end products that we see (and see through) every day. It is manufactured in flat sheets and therefore, does not include bottles or containers. For modern architectural and automotive applications, the flat glass is sometimes bent after production of the plane sheet. Initially produced in plane form, flat glass is commonly used as the starting point for windows, glass doors, transparent walls and windshields.
Depending on the manufacturing process used, flat glass comes either as float glass, sheet glass or rolled glass. Most flat glass is produced by the float process. Annealed glass is the basic flat glass product that is the first result of the float process. It is common glass that tends to break into large, jagged shards. It is used in some end products and often in double-glazed windows. It is also the starting material used to produce more advanced products through further processing such as laminating, toughening/tempering, coating, etc.
Plexiglass is a solid transparent plastic made of polymethyl methacrylate, an acrylic petroleum-based product. This transparent material has thermoplastic properties which allow it to be bent and shaped into a variety of forms. Along with its many advantages over glass in specific uses, it is easier to handle and cut.
Considered shatter-resistant, plexiglass requires far more pressure to crack than a pane of equally thick glass and doesn’t shatter into many dangerous pieces, making it good material for areas where children play, police shields and basketball backboards. Plexiglass allows more than 90% of sunlight and about 80% of shaded light to pass through, making it the clearest material available. No matter how thick it is, plexiglass is always clear and doesn’t create the same high levels of reflection and glare as glass does. UV coatings for protection and color tints can be applied to plexiglass.
Often used as a lightweight (50% lighter than glass) or shatter-resistant alternative to glass, its transparency and durability makes it a versatile material and has been used in a wide range of fields and applications such as: rear-lights and instrument clusters for vehicles, appliances, lenses for glasses and artistic/architectural creativity. Plexiglass affords shatter resistant panels for building windows, skylights, bullet proof security barriers, signs & displays, sanitary ware, bathtub enclosures, LCD screens, furniture, aquariums, spectator protection in ice hockey rinks, business signs and many other applications.
Tempered glass is often referred to as safety glass because it is far more resistant to breakage than normal, annealed glass. Tempered glass is made from annealed glass treated with a thermal tempering process. This controlled thermal treatment increases the strength of annealed glass by creating balanced internal and surface stresses which cause the glass sheet, when broken, to crumble into small granular chunks of similar size instead of splintering into random, jagged shards. These granular chunks are less likely to cause injury.
As a result of its safety and strength, tempered glass is used in a variety of demanding applications, including passenger, side and rear windows in automobiles, shower doors, architectural glass doors and partitions, glass tables and furniture, refrigerator trays, as a component of bulletproof glass, diving masks, and various types of plates and cookware.
Tempered glass is used when strength, thermal resistance and safety are important considerations. The most commonly encountered tempered glass is that used for side and rear windows in automobiles. It is also used in buildings for unframed assemblies (such as frameless doors), structurally loaded applications, and any other application that would become dangerous in the event of human impact.
Laminated glass, also known as toughened glass, is a type of safety glass that holds together when shattered. It is also considered security glass and is used for buildings and automobiles at higher risk of attack.
Usually consisting of layers of tempered or “toughened” glass and plastic, laminated glass consists of two or more layers of glass bonded together by one or more interlayers of a durable polymeric material, often polyvinyl butyral (PVB) or another polymer or resin. This interlayer keeps the layers of glass bonded even when broken, and its high strength prevents the glass from breaking up into large, sharp pieces. This produces a characteristic “spider web” cracking pattern when the impact is not enough to completely pierce the glass.
Laminated glass is normally used when there is a possibility of human impact or where the glass could fall if shattered. It is used extensively in building and housing products (i.e. skylight glazing) and in the automotive and transportation industries. Most building facades and car windshields are made with laminated glass, usually with other technologies incorporated.
In geographical areas requiring hurricane-resistant construction, laminated glass is often used in exterior storefronts, curtain walls and windows. Laminate glass is perfect for aquariums, display cases and anything else requiring safety.
The interlayer also provides a way to apply several other technologies and benefits to laminated glass, such as coloring, tinting to reduce solar heat gain and reduce glare and interior fading, sound dampening (reduce perceived noise by 50%), fire-resistance, UV filtering (screens out 99% of UV rays, equivalent to SPF 50+) and other technologies that can be embedded in or with the interlayer.
Wired glass, also known as wire mesh glass, is sheet glass reinforced with a wire grid or mesh of thin metal wire embedded within the glass. It is utilized for its fire-resistant abilities, and is well-rated to both withstand heat and a hose stream. This is why wired glass is almost exclusively used on service elevators to prevent fire ingress to the shaft and why it is also commonly found in institutional settings which are often well-protected and partitioned against fire.The wire prevents the glass from falling out of the frame even if it cracks under thermal stress, but is far more heat-resistant than a laminating material.
New generation “safety wired” glass products can be used in hazardous locations like doors, sidelites and any location that require safety. Safety wired glass products are tested to and meet the highest safety requirements mandated by both the code and the federal government’s Consumer Products Safety Commission and have attained a fire rating after stringent fire testing.
Model building codes restrict the use of “traditional wired” glass in hazardous locations. Non-safety, traditional wired glass can and has broken with as little as 50 ft. lbs. of force, or the force of a small child running into its glazing. While the presence of the wire mesh appears to be a strengthening component, wired glass is actually half as strong as un-wired annealed glass due to the incursions of the wire into the structure of the glass. Wired glass often may cause heightened injury in comparison to unwired glass, as the wire acts as a break plane and amplifies the irregularity of any glass fractures.
Tinted glass refers to any glass that has been treated with a material such as a film or coating that reduces the transmission of light through it. Glass can be tinted with various types of coating, which block and/or reflect different amounts and types of light, according to the needs and preferences of the consumer.
Tinting can reduce heat by filtering out about 80% of solar heat, versus less than 30% for non-tinted windows. Glare is significantly reduced, which reduces eye strain, fatigue and distractions. Darker tinted windows can reduce UV exposure by 95% or more and your possessions are more hidden, providing increased security.
In automobiles, tinted glass provides an easy solution for drivers seeking occupant privacy and the reduction of heat buildup within the car. The large majority of automotive window films are dark colored (tinted) and can be achieved through three processes. First, film tinting is an inexpensive, aftermarket method where a thin layer is applied to the window glass; it comes in a variety of tints, but can easily crack or peel and can be difficult to remove. Films should always be a major brand, support the manufacture’s warranty and be done by a shop approved through the International Window Film Association (IWFA). Coating tinting involves applying a unique spray to the surface of the glass and should be accomplished by experts due to the difficult application process, but does last longer than films. Instead of applying a film to the glass, OEM tinted glass involves adding a tint to the glass when the glass is made.
OEM tinting is usually lighter and lasts the life of the glass. Always check your local city and state rules on how dark tinting can be and be aware of how it may change your vision at night. “Window film” is a retrofit upgrade that is generally installed to flat glass in existing buildings and address a range of problems inherent to glazing, such as heat and glare reduction, thermal insulation, UV filtration, safety and security, privacy, decoration and graffiti protection. There are many types, grades, shades, colors and thicknesses of window films available, and they are an extremely cost-effective method to reduce heating and cooling costs in existing buildings by reducing the amount of heat transfer through glazing. Window films for commercial installations are typically clear.
While safety glass aims to protect people from injury/loss from natural causes, security glass is intended to protect people within buildings and automobiles from the risk or occurrence of injury or loss from the intentional actions of mankind. For buildings or vehicles exposed to extra risk, security glass can be designed for bullet and blast-resistance, burglary, forced entry and ballistic attacks and blasts.
Tinted, high-performance, fire-rated composites, sound dampening and UV resistance are other options available to meet specific security glass requirements. Standard Laminated Architectural Glass (LAG) provides a significant improvement in resistance to attack from a variety of hand held weapons (rock, hammer, brick, sledgehammer, chisel, ax, etc.) for residential and commercial settings. Impact resistance is directly related to the percentage of interlayer in the laminate and numbers of layers of glass. Also, it cannot be cut from one side, making glass cutters useless.
The interlayer also provides a way to apply several other technologies and benefits to laminated glass, such as coloring, tinting to reduce solar heat gain and reduce glare and interior fading, sound dampening (reduce perceived noise by 50%), fire-resistance, UV filtering (screens out 99% of UV rays, equivalent to SPF 50+) and other technologies that can be embedded in or with the interlayer.